Welcome to the dawn of the next industrial revolution—Industry 4.0. Virginia manufacturers are stepping up their game by adopting cutting-edge technologies like IT network maintenance, driving a paradigm shift in the future of manufacturing. Let’s explore the key aspects of Industry 4.0 and its impact on production facilities in Virginia.
In this blog, we analyze:
- What Industry 4.0 is
- The four key drivers behind Industry 4.0
- The connection between IT network maintenance and Industry 4.0
- Two Virginia case studies of manufacturers doing Industry 4.0 right
What is Industry 4.0?
Industry 4.0, also known as the Fourth Industrial Revolution, is a transformative blend of digital technologies, automation, and data-driven processes in the manufacturing industry. It involves integrating physical systems with digital advancements, inspiring revolutionary changes for large corporations and smaller manufacturing entities.
The term “Industry 4.0” originated in 2011 when the German government used it to describe a manufacturing digitization project. Over time, it evolved into a set of recommendations for implementing technology, emphasizing integrating cyber-physical systems, automation, and smart technology. Klaus Schwab, founder of the World Economic Forum, popularized the term in 2016, highlighting the big shift to industrial capitalism. This revolution blurs the lines between physical, digital, and biological worlds, powering global production facilities and supply networks through automation, IoT, and machine-to-machine communication.
WATCH THE VIDEO: What is Industry 4.0?
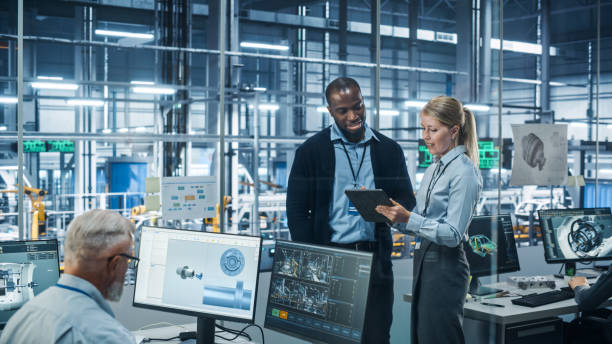
Key Technologies Driving Industry 4.0
- IoT (Internet of Things) Sensors: These collect real-time data to monitor production, enabling early detection of malfunctions within the production line.
- Big Data Analytics: Leveraging data insights to optimize processes, these improve performance and stimulate decision-making.
- Digital Quality Control: Makes sure product quality is up to par through automated inspections and real-time feedback.
- Cybersecurity Programs: Protect critical systems from cyber threats.
The Link Between IT Network Maintenance and Industry 4.0
Industry 4.0 and IT network maintenance go hand in hand. For Industry 4.0 to work, it needs strong and secure IT networks. These networks connect and support advanced technologies like cyber-physical systems, IoT devices, and data analytics. They ensure that everything talks to each other smoothly, data is shared in real time, and systems are constantly monitored. This seamless integration helps make manufacturing processes work smarter and harder.
Industry 4.0 Innovations in Virginia
Even small to mid-sized Virginia manufacturers can practice Industry 4.0 solutions. By adopting these technologies, they can become industry leaders, achieving unbeatable levels of productivity, innovation, and connectivity.
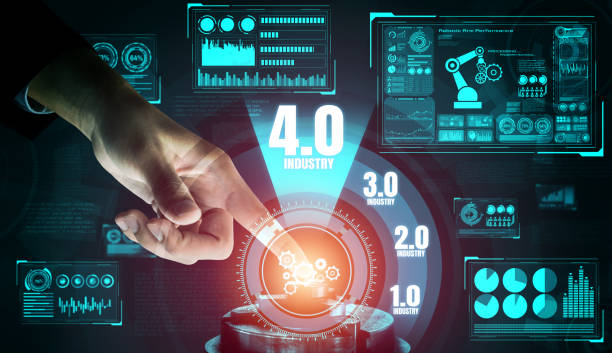
DVTI Case Study
Directed Vapor Technologies (DVTI), based in Charlottesville, Virginia, is a true example of how Industry 4.0 can be successfully implemented. Specializing in advanced coating technology for niche and emerging markets, DVTI faced the challenge of making its core technology available to broader commercial markets.
Collaborating with GENEDGE, a NIST MEP affiliate, DVTI leveraged several strategic solutions like brand realignment, prototyping support, and obtaining quality certification. This partnership yielded impressive results, including an estimated $9 million increase in sales and creating ten new jobs. DVTI’s story demonstrates that even small firms can harness Industry 4.0 innovations to achieve significant market success and operational improvements.
Chesapeake Machine Works, Inc. Case Study
Since 1987, this Chesapeake-based machine shop has provided customized solutions for the Department of Defense and the U.S. Navy.
Faced with new cybersecurity requirements, CMW turned to GENEDGE’s DEFENDCUI-VA program to protect its data and gain a competitive edge. GENEDGE assessed CMW’s compliance levels and helped develop an end-to-end cybersecurity plan.
As a result, CMW anticipated impacts, including $40K in sales, $59.6K in cost savings, $8K in investments, and three jobs created or retained.
How Could I Make My Manufacturing Systems Smarter?
Industry 4.0 goes beyond big tech—it’s about aligning processes, people, and technology to reap its rewards. GENEDGE supports production facilities in Virginia by offering Industry 4.0 consulting services and training programs to help integrate advanced manufacturing technologies and enable them to be more competitive and operational.
We also provide supply chain optimization consultants to streamline and enhance your supply chain processes. Workforce is a critical element, and our manufacturing workforce development services keep your team skilled and ready to handle the latest technological advancements.